India’s Largest Necktie Manufacturer:
Neckties are not just fashion accessories – they are a symbol of elegance, professionalism, and style. At Blue Shine, we take pride in being India’s largest necktie manufacturer, delivering custom-made ties to top fashion brands across the globe.
In this article, we’ll take you behind the scenes and show you the step-by-step process of how we make neckties that meet international standards and client expectations.
🧵 Step-by-Step: How We Manufacture Neckties for Top Brands
1. Understanding the Brand’s Vision
Every brand is unique. Some go for minimalist patterns, while others prefer bold, statement-making designs. We begin by:
- Conducting a detailed consultation with the client.
- Studying their brand identity, color preferences, and design inspiration.
- Finalizing material, design, and packaging options.
✅ Our design team works closely with the brand to ensure every necktie reflects their signature style.
2. Choosing the Right Fabric
Fabric is the soul of a necktie. We offer a wide selection including:
- 100% pure silk
- Premium polyester
- Cotton blends
- Microfiber
Each fabric is tested for texture, durability, and draping quality. Silk ties are the most luxurious, while microfiber offers affordability with style.
✅ We source high-quality raw materials from trusted vendors.
3. Digital Pattern Design
Once the fabric is selected, we move to the design stage:
- Patterns are digitally created using CAD software.
- We can produce stripes, solids, dots, paisley, or custom prints.
- The pattern is aligned according to the grain of the fabric for perfect finish.
✅ Precision in pattern alignment ensures visual balance and brand consistency.
4. Cutting the Fabric
This is a critical step:
- The fabric is cut on the true bias (at a 45° angle) to give the tie flexibility and a smooth drape.
- Each tie typically requires 3 fabric pieces: the blade (front), neck, and tail (back).
- Laser-guided machines ensure perfect cuts every time.
✅ Cutting on the bias prevents the tie from twisting or curling.
5. Adding the Interlining
The interlining gives the tie its structure and weight:
- We use premium wool or poly-wool blends depending on the tie type.
- Interlining is matched to fabric thickness and tie style.
- It is hand-positioned and sewn securely between the layers.
✅ A good interlining ensures a sharp knot and lasting shape.
6. Hand Stitching and Finishing
Our expert craftsmen hand-finish every necktie:
- Ties are folded, sewn, and stitched with a slip stitch for flexibility.
- The bar tack is added at both ends to reinforce the structure.
- Tipping (the fabric at the back end) is either custom-branded or plain.
✅ Hand-stitching gives each tie a touch of class and durability.
7. Quality Control
Every tie goes through 3 layers of quality inspection:
- Visual check for stitching defects.
- Measurements check (length, width, knot area).
- Final packaging inspection.
✅ Only flawless ties are approved for shipping.
8. Custom Branding and Packaging
For top brands, packaging matters as much as the product:
- We provide custom-printed brand labels, barcodes, and tags.
- Ties are packed in eco-friendly boxes, pouches, or sleeves as per client request.
- Bulk orders are packed for safe transportation.
✅ We help brands deliver a premium unboxing experience to their customers.
🔝 Why Top Brands Choose Blue Shine
- ✅ 25+ years of experience
- ✅ Export-quality standards
- ✅ Modern manufacturing units in India
- ✅ In-house design & sampling team
- ✅ Custom orders starting from low MOQ
- ✅ Fast turnaround & global shipping
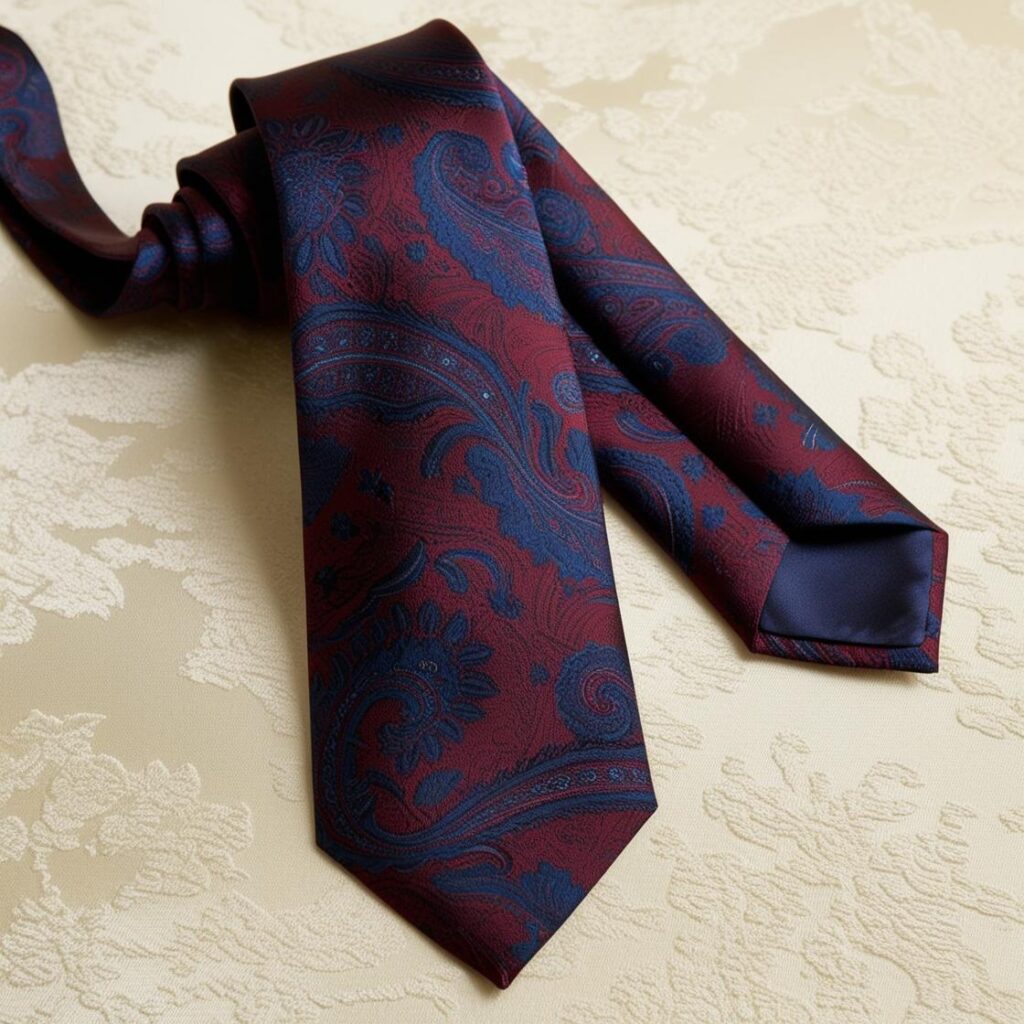
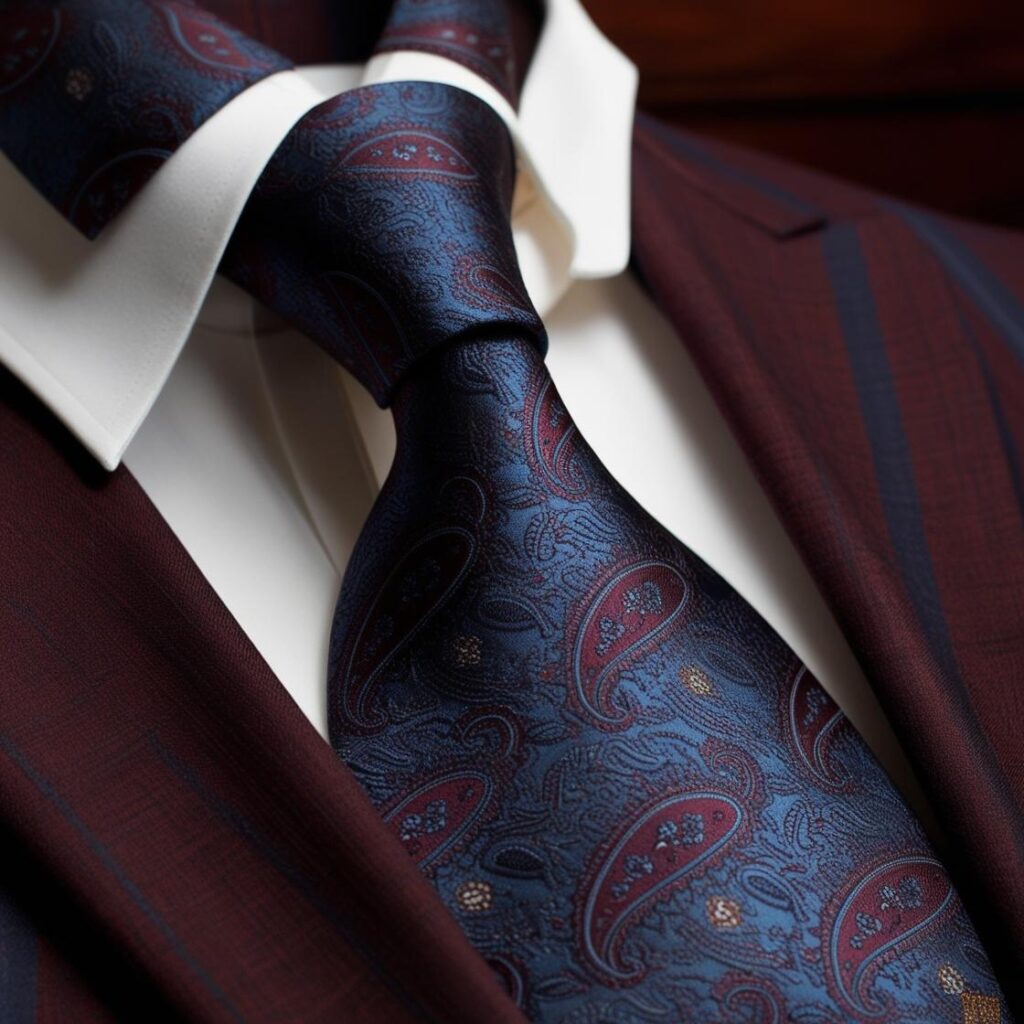
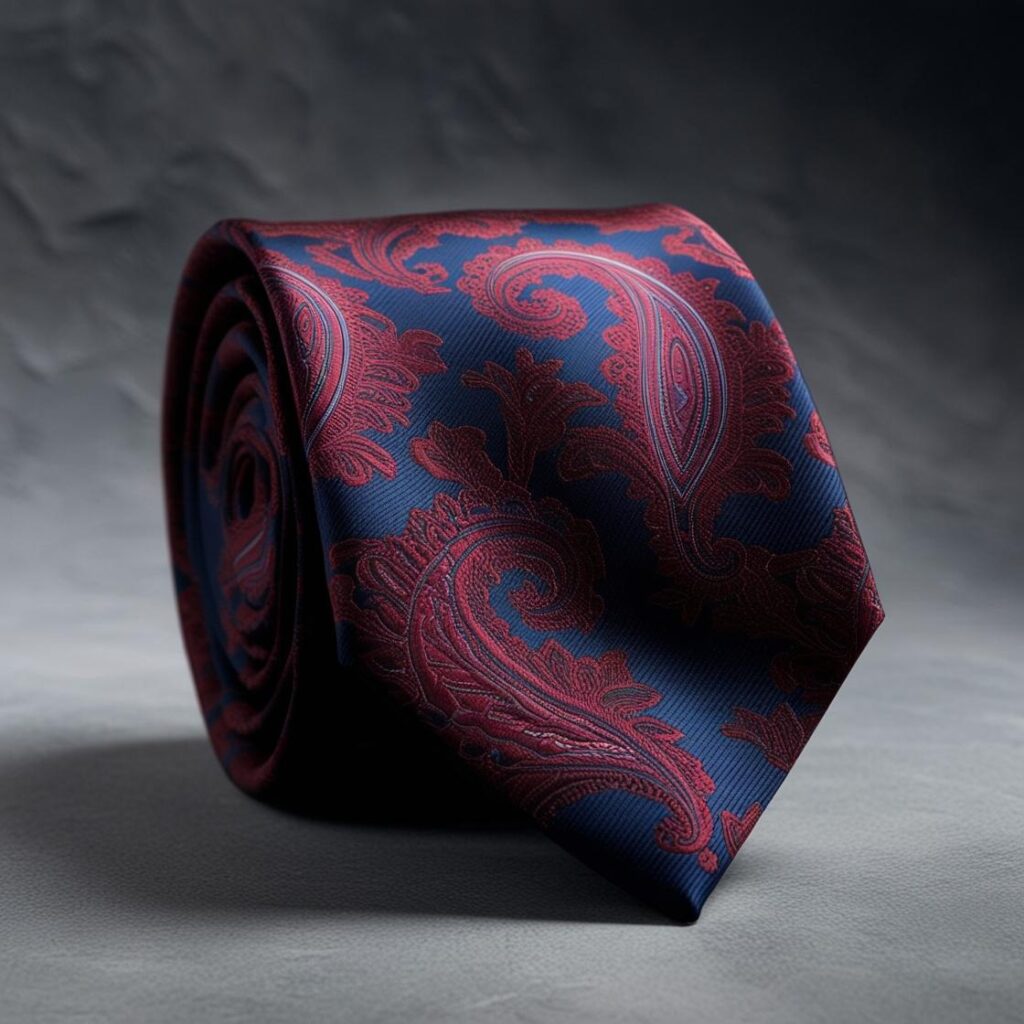
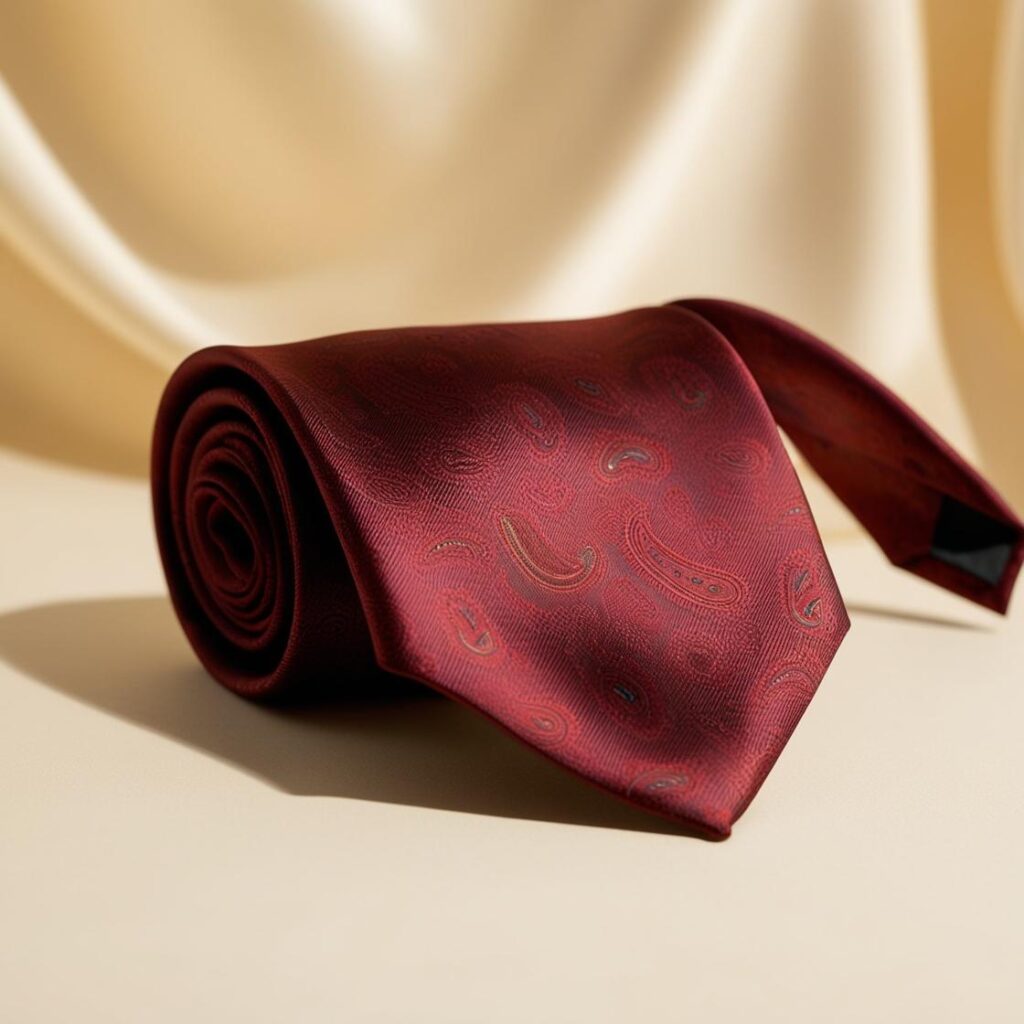
We don’t just manufacture ties — we help build fashion identities for brands.
🎯 Final Words
India’s Largest Necktie Manufacturer:
At Blue Shine, we believe that every necktie tells a story. From fabric selection to hand-stitching to final packaging — we maintain strict quality and creativity at every step.
That’s how we make neckties that stand out in stores, offices, and runways across the world.